Properties of Bismaleimide Resin,
Bismaleimide Resin
2.Properties of Bismaleimide Resins
Here are the physical properties of bismaleimide resins:
Thermal Stability:
High Glass Transition Temperature (Tg): Typically ranging from 220°C to 300°C.
Decomposition Temperature: Generally above 400°C, indicating excellent thermal stability.
Mechanical Properties:
High Strength: Good tensile and compressive strength.
Toughness: Moderate to high toughness compared to other high-performance resins.
Elastic Modulus: High modulus, providing rigidity.
Electrical Properties:
Dielectric Constant: Low to moderate, which is beneficial for electronic applications.
Dielectric Loss: Low, ensuring minimal energy dissipation in electrical fields.
Volume Resistivity: High, indicating good insulation properties.
Chemical Resistance:
Solvent Resistance: Excellent resistance to many organic solvents.
Chemical Stability: Stable against many chemicals, making them suitable for harsh environments.
Moisture Absorption:
Low Moisture Absorption: Typically less than 1%, which helps maintain mechanical and electrical properties under humid conditions.
Processing Properties:
Curing: Can be cured at relatively high temperatures (typically 180-250°C) with a post-cure to achieve optimal properties.
Moldability: Good mold flow characteristics, allowing for the manufacture of complex shapes and high precision components.
Density:
Typically ranges from 1.25 to 1.35 g/cm³, depending on the specific formulation and fillers used.
3.Applications
Aerospace: Used in the manufacturing of high-temperature resistant composite parts, such as engine components, airframes, and heat shields.
Automotive: Utilized in making lightweight, high-strength components that can withstand high temperatures, such as under-the-hood parts.
Electronics: Employed in the production of printed circuit boards (PCBs) and other electronic components that require good thermal and electrical properties.
Industrial: Used in the production of high-performance adhesives, coatings, and moldings that require durability and resistance to extreme conditions.
4.Processing and Curing
Bismaleimide resins typically undergo a curing process involving heat and sometimes pressure. The curing can be done via:
Thermal Curing: Heating the resin to a specific temperature to initiate the cross-linking process.
Catalytic Curing: Using catalysts to reduce the curing temperature and time.
Autoclave Curing: Applying both heat and pressure in an autoclave to produce high-strength composite materials.
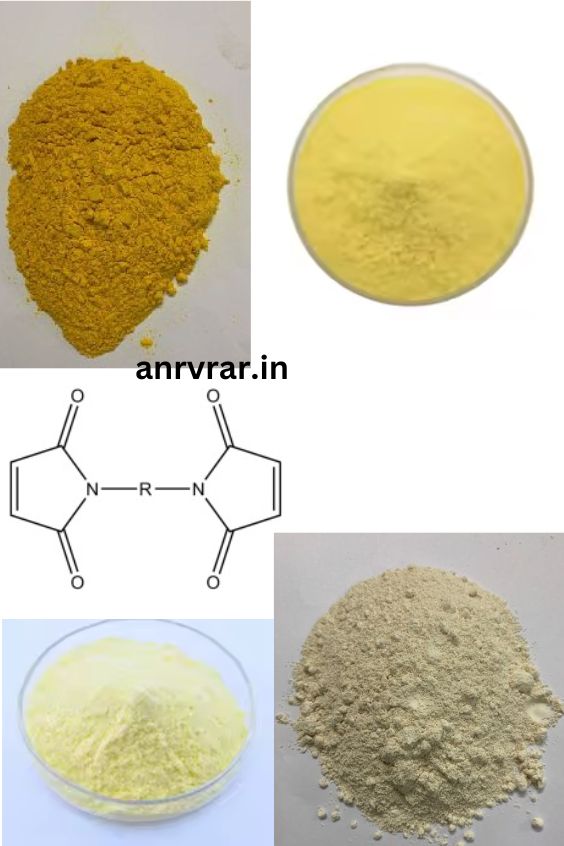
5.Industrial Uses of Bismaleimide resins.
Here are some of the primary industrial uses of BMI resins:
Aerospace Industry:
Composite Materials: Used in the fabrication of high-performance composite materials for aircraft structures, including fuselage panels, wings, and tail sections.
Heat-Resistant Components: Employed in the production of components that require high thermal stability and strength, such as engine nacelles and heat shields.
Automotive Industry:
Under-the-Hood Components: Used for components exposed to high temperatures, such as engine covers, intake manifolds, and heat shields.
Structural Parts: Employed in the manufacture of lightweight, high-strength structural parts to improve fuel efficiency and performance.
Electronics Industry:
Printed Circuit Boards (PCBs): Utilized in high-frequency and high-performance PCBs due to their low dielectric constant and excellent electrical insulation properties.
Electronic Packaging: Used in advanced electronic packaging materials for protecting sensitive components against thermal and mechanical stress.
Industrial Machinery:
Gears and Bearings: Used in the production of gears, bearings, and other mechanical components that require high wear resistance and stability at elevated temperatures.
Seals and Gaskets: Employed in making high-performance seals and gaskets that can withstand aggressive chemicals and high temperatures.
Marine Industry:
Marine Structures: Used in the construction of high-strength, corrosion-resistant marine structures, such as hulls, decks, and other critical components of boats and ships.
Offshore Applications: Employed in offshore oil and gas platforms for components exposed to harsh environmental conditions.
Defense Industry:
Weapon Systems: Used in missile casings, rocket motor casings, and other high-temperature, high-stress components.
Protective Gear: Employed in manufacturing protective gear and armor that require a combination of high strength and lightweight properties.
Energy Sector:
Wind Turbine Blades: Utilized in the production of wind turbine blades that require high strength, stiffness, and durability.
Oil and Gas: Employed in downhole drilling tools and components that must withstand extreme temperatures and pressures.
Sporting Goods:
High-Performance Equipment: Used in manufacturing high-performance sporting goods such as tennis rackets, golf clubs, and bicycle frames, where lightweight and high strength are crucial.
6.Manufacturing Process of Bismaleimide resins
Synthesis of Bismaleimide Monomers:
Maleic Anhydride Reaction: The process starts with the reaction of maleic anhydride with diamines. Maleic anhydride is reacted with a primary amine (R-NH2) to form maleamic acid intermediates.
Cyclodehydration: These intermediates undergo cyclodehydration (a dehydration reaction that forms a cyclic imide) to produce the bismaleimide monomers. This step is typically catalyzed by an acid or carried out under heat to remove water.
Purification:
The bismaleimide monomers are purified to remove any unreacted starting materials or byproducts. This can be achieved through crystallization, recrystallization, or solvent extraction techniques.
Formulation:
Additives and Fillers: The purified bismaleimide monomers are mixed with various additives and fillers to enhance their properties. Common additives include catalysts, stabilizers, and plasticizers. Fillers can be inorganic materials like silica or carbon fibers to improve mechanical strength and thermal stability.
Prepolymer Formation: In some cases, a prepolymer (partially polymerized resin) is created to improve processing characteristics. This is done by partially curing the bismaleimide monomers under controlled conditions.
Polymerization:
Mixing and Blending: The formulated resin mixture is thoroughly mixed and blended to ensure uniform distribution of additives and fillers.
Curing: The mixture is then cured, which involves polymerizing the bismaleimide monomers to form a cross-linked thermoset polymer. Curing can be initiated by heat (thermal curing) or radiation (UV curing), depending on the formulation. The curing process typically involves:
Initial Heating: The mixture is heated to a specific temperature to initiate polymerization. This temperature is usually between 150°C and 200°C.
Post-Curing: After the initial cure, the material is often subjected to a higher temperature (200°C to 250°C) for a prolonged period to complete the polymerization and achieve optimal properties.
Molding and Shaping:
Molding Techniques: The curing process can be integrated with molding techniques such as compression molding, transfer molding, or resin transfer molding (RTM) to shape the resin into the desired form.
Composite Fabrication: For composite materials, bismaleimide resin is often impregnated into fiber reinforcements (like carbon fiber or glass fiber) before curing, using processes such as filament winding, lay-up, or pultrusion.
Post-Processing:
Machining and Finishing: After curing, the final BMI resin product may undergo machining or finishing operations to achieve precise dimensions and surface quality.
Quality Control: The finished products are subjected to rigorous quality control tests to ensure they meet the required specifications and performance standards. These tests may include mechanical testing, thermal analysis, and chemical resistance evaluations.
7.Advantages and Challenges
Advantages:
High thermal and mechanical performance
Excellent chemical and moisture resistance
Superior electrical insulating properties
Challenges:
Relatively high cost compared to other resins like epoxy or polyester
Processing difficulties due to high curing temperatures and the need for specialized equipment
Brittleness, which can be mitigated by toughening with additives or by hybridizing with other resins
FAQ of Bismaleimide (BMI) Resins
1.What are Bismaleimide (BMI) resins?
Bismaleimide resins are a class of high-performance thermosetting polymers known for their excellent thermal stability, mechanical strength, and chemical resistance. They are widely used in aerospace, automotive, electronics, and other demanding applications.
2.What advantages do BMI resins offer over other resins?
BMI resins offer superior thermal stability, mechanical strength, and chemical resistance compared to many other thermosetting resins like epoxies. They maintain their properties at higher temperatures and in harsh chemical environments, making them suitable for high-performance applications.
3.How are BMI resins synthesized?
The synthesis involves reacting maleic anhydride with diamines to form maleamic acid intermediates, which are then cyclodehydrated to produce bismaleimide monomers. These monomers are purified and mixed with additives and fillers before being polymerized through thermal curing.
4.Can BMI resins be customized for specific applications?
Yes, BMI resins can be tailored with various additives, fillers, and processing techniques to meet specific application requirements, such as enhanced toughness, reduced brittleness, or improved processing characteristics.