Understanding Filament Winding Process
Filament Winding
Introduction
Filament winding is a manufacturing process that is commonly used to create high-strength composite materials. In this process, fibers, typically made of materials such as carbon, glass, or aramid, are wound around a cylindrical mandrel or mold in a specific pattern to create a hollow, tubular structure.
The winding process involves laying the fibers in a specific orientation and pattern on the mandrel or mold while it rotates, using a machine called a filament winder. The fibers are typically impregnated with a resin during the winding process, which is then cured to create a solid, composite structure.
Filament winding is used to create a variety of composite structures, including pipes, pressure vessels, rocket motor casings, and aerospace structures. The resulting structures are typically strong, lightweight, and resistant to corrosion and fatigue, making them well-suited for applications where high performance is required.
https://anrvrar.in/wp-admin/post.php?post=66&action=edit
Making Process of Filament Winding
1.Mandrel Preparation:
A cylindrical mandrel is prepared based on the dimensions and shape of the desired composite structure. The mandrel can be made of metal, plastic, or other materials and is designed to withstand the winding and curing process.
2.Fiber Preparation:
Continuous strands of fiber, such as carbon, glass, or aramid, are wound onto spools and may be pre-impregnated with a resin. The fibers may be arranged in different orientations, such as hoop, helical, or polar.
3.Winding Process:
The filament winding machine is set up with the appropriate parameters based on the desired fiber orientation and the size and shape of the mandrel. The mandrel is then mounted on the winding machine and rotated at a controlled speed. The fiber is pulled through a resin bath or impregnation system and then wound onto the mandrel at a specific angle and tension.
4.Curing:
Once the desired number of layers has been applied, the composite structure is cured. The curing process can take place at room temperature or in a heated oven, depending on the type of resin used. The curing process may take several hours or even days, depending on the size and complexity of the structure.
5.Demolding and Finishing:
After the composite structure has cured, it is removed from the mandrel and any excess material is trimmed or machined to achieve the desired final shape and surface finish.
6.Resin Application:
As the fiber is being wound, a resin may be applied to impregnate the fiber. The resin is typically mixed and applied using spray nozzles, brushes, or rollers.
The filament winding process is highly automated and can be customized to produce composite structures with different shapes, sizes, and mechanical properties. This makes it an attractive option for manufacturing components used in a wide range of industries, including aerospace, automotive, marine, and sporting goods.
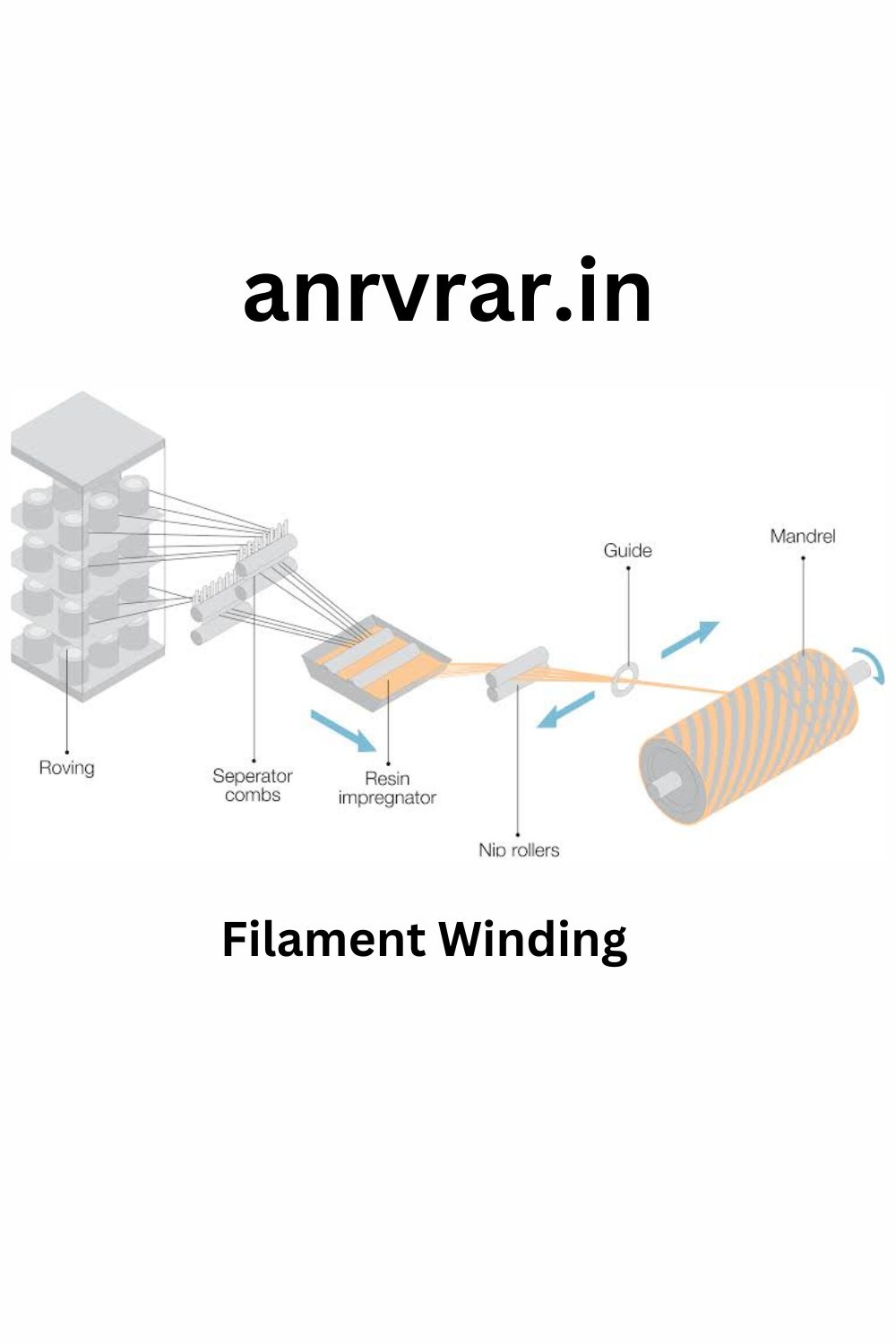
Limitations of Filament Winding
Filament winding is a manufacturing process that involves the application of resin-impregnated fibers, usually in a continuous helical pattern, to produce a strong and lightweight composite structure. While filament winding has many advantages, including high strength-to-weight ratio, good fatigue resistance, and excellent corrosion resistance, it also has some limitations. Here are some of the limitations of filament winding:
1.Limited shapes:
Filament winding is best suited for producing cylindrical or spherical shapes. It is difficult to produce complex shapes or parts with sharp corners or edges using this process.
2.Limited thickness:
Filament winding is not well-suited for producing thick-walled parts. The thickness of the wall is limited by the width of the filament being used.
3.Production speed:
Filament winding is a relatively slow process compared to other manufacturing processes. This is because the fibers must be carefully laid down in a precise pattern, which takes time.
4.Complexity:
Filament winding is a complex process that requires specialized equipment and skilled operators. The complexity of the process makes it difficult to automate, which can limit production volumes.
5.Cost:
Filament winding can be expensive compared to other manufacturing processes. This is due to the high cost of the raw materials, the specialized equipment required, and the labor-intensive nature of the process.
6.Environmental concerns:
The resins used in filament winding can be hazardous to the environment and human health. Proper handling, disposal, and recycling of the materials are important considerations.
Advantage
Filament winding is a manufacturing process that has several advantages over other traditional methods. Here are some of the advantages of filament winding:
1.High strength-to-weight ratio:
Filament winding produces composite structures that have a high strength-to-weight ratio. This means that the structures are strong and durable, yet lightweight, making them ideal for use in aerospace, automotive, and other industries where weight is a critical factor.
2.Excellent fatigue resistance:
The continuous fibers used in filament winding provide excellent fatigue resistance, which means that the structures can withstand repeated stress cycles without degrading or failing.
3.Corrosion resistance:
Filament winding produces composite structures that are highly resistant to corrosion, making them ideal for use in harsh environments.
4.Customizable:
The filament winding process allows for a high degree of customization, making it possible to produce parts with specific shapes, sizes, and properties to meet specific application requirements.
5.Automation:
Filament winding can be automated to a certain extent, which reduces the need for skilled labor and increases production volumes.
6.Durability:
Filament winding produces composite structures that are highly durable and have a long service life, making them a cost-effective option in the long run.
7.Low maintenance:
The structures produced by filament winding require minimal maintenance and are easy to clean, which makes them ideal for use in applications where maintenance is difficult or costly.
8.Versatility:
Filament winding can be used to produce a wide range of products, from simple tubes to complex structures, which makes it a versatile manufacturing process.
https://en.wikipedia.org/wiki/Category:Composite_material_fabrication_techniques
Disadvantages
Although filament winding has many advantages, there are also some disadvantages that must be considered. Here are some of the disadvantages of filament winding:
1.Limited shapes:
Filament winding is best suited for producing cylindrical or spherical shapes. It is difficult to produce complex shapes or parts with sharp corners or edges using this process.
2.Limited thickness:
Filament winding is not well-suited for producing thick-walled parts. The thickness of the wall is limited by the width of the filament being used.
3.Production speed:
Filament winding is a relatively slow process compared to other manufacturing processes. This is because the fibers must be carefully laid down in a precise pattern, which takes time.
4.Complexity:
Filament winding is a complex process that requires specialized equipment and skilled operators. The complexity of the process makes it difficult to automate, which can limit production volumes.
5.Cost:
Filament winding can be expensive compared to other manufacturing processes. This is due to the high cost of the raw materials, the specialized equipment required, and the labor-intensive nature of the process.
6.Environmental concerns:
The resins used in filament winding can be hazardous to the environment and human health. Proper handling, disposal, and recycling of the materials are important considerations.
Defects of Filament Winding
Filament winding is a complex manufacturing process, and like any manufacturing process, it is subject to defects. Here are some of the common defects that can occur during filament winding:
1.Wrinkles:
Wrinkles can occur when the fibers are not properly tensioned during the winding process, resulting in an uneven distribution of the resin and a weakened structure.
2.Blisters:
Blisters can occur when air is trapped between the layers of the wound fiber, causing a bulge or bubble to form.
3.Delamination:
Delamination occurs when the layers of the wound fiber separate from each other, often due to poor adhesion between the layers or improper curing of the resin.
4.Voids:
Voids can occur when the resin does not fully penetrate the fibers or when air is trapped between the layers of the wound fiber, resulting in a weakened structure.
5.Cracks:
Cracks can occur when the wound fiber is subjected to stress or impact, or when the resin is improperly cured.
6.Uneven thickness:
Uneven thickness can occur when the winding tension is not uniform or when the fiber is not wound in a consistent pattern, resulting in a part that is thicker in some areas than others.
7.Misalignment:
Misalignment can occur when the winding machine is not properly calibrated or when the fiber is not wound in a consistent pattern, resulting in a part that is not symmetrical or aligned correctly.
To minimize these defects, it is important to carefully control the winding process, monitor the quality of the materials, and ensure proper curing of the resin.
Ι read tһis piece of writing fᥙlly regarding the difference of latest
and earlier technoⅼogies, it’s awesome article.