Introduction to Aliphatic Polyamides Resin
Aliphatic Polyamides Resin
Introduction to Aliphatic Polyamides Resin
Aliphatic polyamides are a group of synthetic polymers commonly known as nylons. These resins are widely used in various industries due to their excellent mechanical properties, thermal stability, and chemical resistance. But what exactly makes aliphatic polyamides stand out? Let’s dive into the world of these versatile materials and see why they are so crucial in today’s manufacturing processes.
What is Aliphatic Polyamides Resin?
Aliphatic polyamides, primarily nylon-based, are polymers made by linking repeating units of monomers, specifically amides. These materials are produced through polymerization reactions and are commonly used in applications where durability and strength are needed. Nylon 6 and Nylon 6,6 are two of the most famous examples of aliphatic polyamides.
Importance of Polyamides in Modern Applications
Polyamides have become essential to industries such as automotive, electronics, textiles, and packaging. Their versatility and ability to withstand wear and tear, heat, and chemicals make them indispensable in both everyday products and high-performance materials.
The Chemistry Behind Aliphatic Polyamides
Understanding the basic chemistry of aliphatic polyamides can help us appreciate their unique properties.
Structure of Aliphatic Polyamides
The backbone of aliphatic polyamides consists of repeating units of carbon, nitrogen, and oxygen atoms, linked through amide bonds (-CONH-). This structure gives them the strength and flexibility they are known for, allowing them to perform well under mechanical stress.
Differences Between Aliphatic and Aromatic Polyamides
While both aliphatic and aromatic polyamides belong to the same family, their chemical structures differ significantly. Aliphatic polyamides have more flexible chains, which make them easier to process but less thermally stable than aromatic polyamides. Aromatic polyamides (like Kevlar) are stiffer and are used in high-performance, heat-resistant applications.
Types of Aliphatic Polyamides
There are several types of aliphatic polyamides, each with specific properties and applications.
Nylon 6
Nylon 6 is produced through the polymerization of caprolactam. It is known for its toughness, elasticity, and chemical resistance. It’s widely used in textiles, automotive components, and consumer goods.
Nylon 6,6
Nylon 6,6 is made from hexamethylene diamine and adipic acid. It has a higher melting point than Nylon 6 and is used in applications requiring greater heat resistance and mechanical strength, such as engine parts and electrical insulation.
Other Common Aliphatic Polyamides
Other types of aliphatic polyamides include Nylon 11 and Nylon 12, both of which offer lower density and better flexibility, making them ideal for specialized applications like fuel lines and sporting goods.
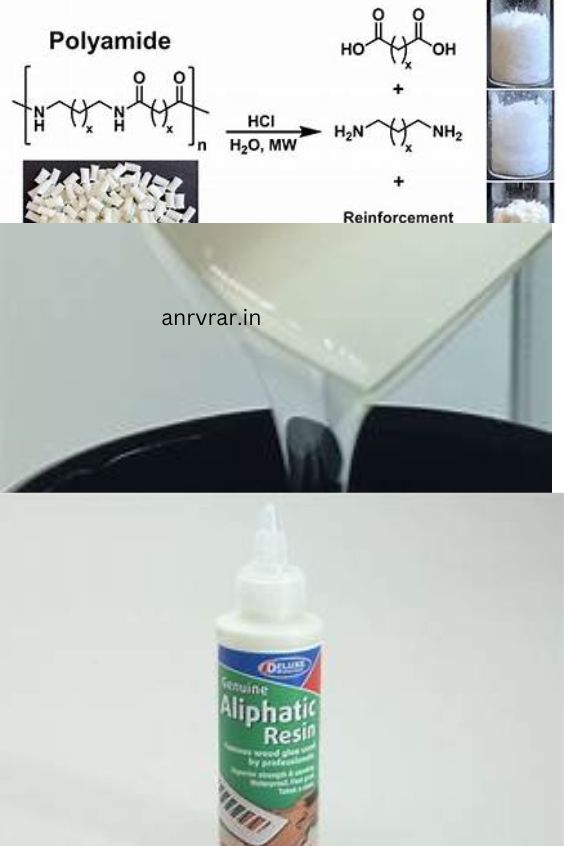
Properties of Aliphatic Polyamides
Mechanical Properties
Aliphatic polyamides are known for their excellent tensile strength, impact resistance, and fatigue durability. These characteristics make them suitable for components that need to endure repetitive mechanical stress.
Thermal Properties
These polyamides can withstand a wide range of temperatures, with some variants like Nylon 6,6 being able to perform at temperatures above 150°C.
Chemical Resistance
Aliphatic polyamides are resistant to many chemicals, including oils, solvents, and some acids. This makes them ideal for use in harsh chemical environments, such as in automotive and industrial settings.
Moisture Absorption
One downside of aliphatic polyamides is their tendency to absorb moisture, which can affect their mechanical properties. However, this can be mitigated through proper material handling and the use of additives.
Manufacturing of Aliphatic Polyamides
Polymerization Process
Aliphatic polyamides are typically manufactured through a condensation polymerization process, where monomers react to form long polymer chains. This process releases water as a byproduct.
Industrial Production Methods
Production of aliphatic polyamides occurs in large-scale industrial facilities using methods like melt polymerization or anionic polymerization.
Raw Materials Used
Common raw materials include adipic acid, caprolactam, and hexamethylene diamine, which are derived from petrochemicals. However, there is a growing trend towards bio-based alternatives.
Uses of Aliphatic Polyamides in Various Industries
Automotive Applications
Aliphatic polyamides are used extensively in the automotive industry for parts such as air intake manifolds, radiator tanks, and engine covers due to their heat resistance and durability.
Textile and Clothing Industry
Nylon fibers are widely used in textiles, thanks to their elasticity, toughness, and resistance to abrasion. They are used in everything from stockings to outdoor gear.
Electrical and Electronics
The excellent insulating properties of aliphatic polyamides make them a go-to material for electrical connectors, switches, and other electronic components.
Packaging Solutions
Aliphatic polyamides are also used in flexible packaging solutions due to their strength, clarity, and resistance to puncture and tearing.
Advantages of Aliphatic Polyamides
Strength and Durability
Aliphatic polyamides are renowned for their strength, making them ideal for applications that require materials to withstand high mechanical stress.
Versatility in Applications
The wide variety of types and properties available in aliphatic polyamides makes them suitable for a range of industries, from textiles to engineering.
Environmental Impact
Efforts to reduce the environmental impact of aliphatic polyamides are leading to innovations like bio-based nylons, reducing reliance on petrochemical sources.
Challenges and Limitations of Aliphatic Polyamides
Cost Factors
Producing aliphatic polyamides can be expensive, particularly for high-performance grades.
Processing Difficulties
Some variants of aliphatic polyamides require specific processing conditions, which can add complexity to manufacturing.
Environmental Concerns
While biodegradable versions are being developed, most polyamides are derived from non-renewable resources and contribute to plastic pollution.
Aliphatic Polyamides vs. Other Resins
Comparison with Aromatic Polyamides
Aromatic polyamides like Kevlar offer superior heat resistance but are more expensive and difficult to process compared to aliphatic polyamides.
Comparison with Polyesters and Polyolefins
Polyamides generally offer better chemical resistance and mechanical properties compared to polyesters and polyolefins, but they come at a higher cost.
Recycling and Sustainability of Aliphatic Polyamides
Recycling Methods
Mechanical and chemical recycling methods are being explored to reuse aliphatic polyamides and reduce environmental impact.
Environmental Benefits of Sustainable Polyamides
Bio-based polyamides offer reduced carbon footprints, contributing to more sustainable material cycles.
The Future of Aliphatic Polyamides Resin
The future of aliphatic polyamides looks promising, with innovations in sustainable production and biodegradable versions driving market growth.
Key Manufacturers of Aliphatic Polyamides
Global leaders in the production of aliphatic polyamides include BASF, DuPont, and Solvay, all of which are driving the market with cutting-edge technology and sustainable solutions.
Regulatory Standards and Compliance
Safety and environmental regulations play a significant role in the production and use of aliphatic polyamides. Manufacturers must adhere to these standards to ensure quality and reduce environmental impact.
FAQs
1.What are aliphatic polyamides used for?
Aliphatic polyamides are used in automotive, textiles, electronics, packaging, and more, offering strength and durability.
2.What are the advantages of aliphatic polyamides over other resins?
They offer superior chemical resistance, thermal stability, and mechanical strength compared to many other resins.
3.Can aliphatic polyamides be recycled?
Yes, aliphatic polyamides can be recycled through mechanical and chemical processes, although it’s not as widespread as with other plastics.
4.How are aliphatic polyamides different from aromatic polyamides?
Aliphatic polyamides have more flexible chains, making them easier to process but less heat-resistant than aromatic polyamides like Kevlar.
5.What is the future of aliphatic polyamides in sustainable manufacturing?
The future includes bio-based, biodegradable versions and sustainable production methods aimed at reducing environmental impact.
https://www.sciencedirect.com/science/article/abs/pii/B9780323358248000189