C-Glass Fibers,Limitations of C-Glass Fiber,
C-Glass Fibers
Introduction
In the ever-evolving landscape of materials used in various industries, C-Glass fibers have emerged as a reliable and versatile option. Comprising a unique composition, these fibers boast exceptional strength, durability, and chemical resistance, making them a popular choice in construction, automotive, and electronics sectors.C-Glass fibers, short for continuous glass fibers, are a type of reinforced fiber known for their composition, which includes calcium oxide and alumina. These fibers play a pivotal role in enhancing the properties of materials they reinforce.
Characteristics of C-Glass Fibers
In the realm of advanced materials, C-Glass fibers stand out as versatile and indispensable components. Understanding the unique characteristics of these fibers is crucial for industries ranging from construction to manufacturing. Let’s dive into the key attributes that make C-Glass fibers a game-changer.
Superior Strength and Durability
C-Glass Fibers: The Powerhouse of Structural Integrity
C-Glass fibers boast exceptional strength, making them a preferred choice for applications demanding structural integrity. From reinforced concrete to composite materials, these fibers enhance the durability and longevity of the end product.
Chemical Resistance
Defying Corrosion: C-Glass Fibers in Hostile Environments
One standout feature of C-Glass fibers is their remarkable resistance to chemical corrosion. This characteristic makes them ideal for applications where exposure to harsh chemicals is inevitable, ensuring longevity and performance in challenging environments.
Thermal Stability
Heat-Resistant Marvels: C-Glass Fibers in Extreme Temperatures
C-Glass fibers excel in maintaining their structural integrity under high temperatures. Industries requiring materials to withstand intense heat, such as aerospace and automotive, turn to these fibers for their unparalleled thermal stability.
Electrical Insulation
Shock-Proof Solutions: C-Glass Fibers in Electrical Applications
The excellent electrical insulation properties of C-Glass fibers position them as key players in electronic and electrical applications. Their ability to resist electrical currents makes them invaluable in the creation of insulating materials for various devices.
Manufacturing Processes
Adaptable Craftsmanship: C-Glass Fibers Shaping the Future
C-Glass fibers offer manufacturers a versatile material that seamlessly integrates into different production processes. Whether in weaving, pultrusion, or molding, these fibers provide flexibility, allowing for the creation of complex structures with ease.
Eco-Friendly Footprint
Green Engineering: C-Glass Fibers in Sustainable Practices
Embracing sustainability, C-Glass fibers contribute to eco-friendly practices. Their longevity and recyclability make them an eco-conscious choice, aligning with the global shift towards greener manufacturing and construction methods.
Conclusion: Harnessing the Power of C-Glass Fibers
In conclusion, the characteristics of C-Glass fibers make them indispensable in a variety of industries. From enhancing structural integrity to withstanding harsh environments, these fibers continue to shape the landscape of modern materials. As industries evolve, the role of C-Glass fibers as a reliable and versatile component remains unwavering.
Applications of c-glass fibre
Construction
In the realm of construction, c-glass fiber plays a pivotal role in reinforcing concrete structures. From bridges to high-rise buildings, its high tensile strength and resistance to corrosion make it a reliable choice, ensuring longevity and stability.
Automotive Strength
When it comes to the automotive industry, c-glass fiber is a game-changer. Used in manufacturing lightweight components, it enhances fuel efficiency without compromising on strength. Car enthusiasts and environmentalists alike celebrate its contribution to creating sleek and robust vehicles.
Aerospace
Aerospace engineers have embraced c-glass fiber for its exceptional properties. From aircraft components to spacecraft applications, its lightweight nature coupled with robustness contributes to the efficiency and safety of airborne vehicles.
Marine
C-glass fiber’s resistance to water and corrosion makes it an ideal candidate for marine applications. Boats, yachts, and maritime structures benefit from its durability, ensuring a prolonged lifespan even in harsh marine environments.
Electronics and Telecommunications
In the fast-paced world of electronics, c-glass fiber is instrumental in the production of cables and connectors. Its high electrical insulation properties and data transmission efficiency contribute to the seamless connectivity we rely on in our digital age.
Sports Equipment
Athletes pushing their limits often rely on sports equipment reinforced with c-glass fiber. From tennis rackets to bicycles, its lightweight yet robust characteristics provide athletes with the edge they need to excel in their respective fields.
Renewable Energy
In the pursuit of sustainable energy, c-glass fiber finds applications in wind turbine blades and solar panels. Its ability to withstand extreme weather conditions ensures the reliability of renewable energy sources.
Military and Defense Securing with Strength
C-glass fiber’s durability and high strength make it an essential component in military and defense applications. From protective gear to ballistic panels, it plays a crucial role in ensuring the safety of personnel in high-risk situations.
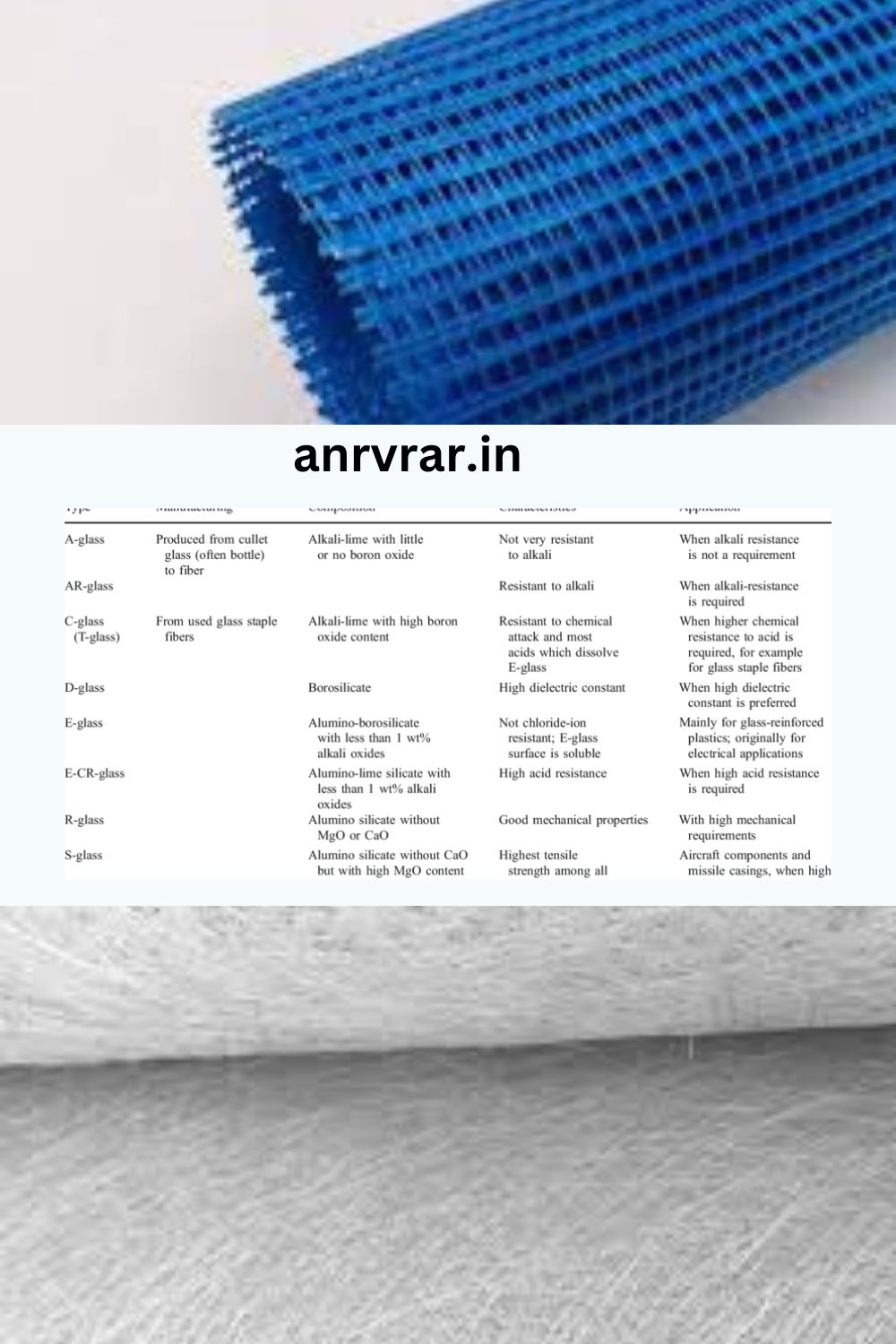
Manufacturing Process
Raw Materials Selection
To ensure the creation of top-tier C-Glass Fiber, the process commences with the careful selection of high-quality raw materials. Fine silica sand, limestone, soda ash, and alumina are meticulously chosen to lay the foundation for a superior end product. This critical step sets the stage for the subsequent manufacturing stages.
Melting and Formation of Molten Glass
The chosen raw materials undergo a transformative process, entering high-temperature furnaces where they are subjected to intense heat. This results in the creation of a molten glass mixture, a crucial precursor to the formation of C-Glass Fiber. The molten glass is carefully monitored and adjusted to achieve the desired viscosity and chemical composition.
Fiber Formation
Once the molten glass achieves optimal conditions, it enters the heart of the manufacturing process—the fiber formation stage. This involves drawing the molten glass into thin fibers through a process known as attenuation. Advanced machinery and technology play a pivotal role in ensuring the precision and uniformity of the fibers, a hallmark of C-Glass Fiber’s exceptional quality.
Coating Performance
To elevate the fiber’s capabilities, a specialized coating is applied. This coating serves multiple purposes, including enhancing resistance to environmental factors, improving adhesion properties, and bolstering overall durability. The careful application of this coating distinguishes C-Glass Fiber, making it a preferred choice in various industries.
Cooling and Collection
As the coated fibers emerge, they undergo a controlled cooling process to solidify their structure. Subsequently, the fibers are meticulously collected, forming the basis for the final product. This stage requires a delicate balance of temperature control and handling precision to ensure the fibers retain their intended characteristics.
Cutting and Sizing
Precision is paramount in crafting C-Glass Fiber to meet diverse industrial needs. The collected fibers undergo cutting and sizing processes, where they are tailored to specific lengths and dimensions. This customization ensures that the final product aligns seamlessly with the requirements of various applications.
Quality Control
At every juncture of the manufacturing process, stringent quality control measures are implemented. Cutting-edge technologies and skilled technicians work in tandem to conduct thorough inspections, guaranteeing that each batch of C-Glass Fiber meets or exceeds industry standards.
Advantages of C-Glass Fibers
In the dynamic landscape of material science, C-Glass fibers stand out as a robust and versatile solution, offering a myriad of advantages that propel them to the forefront of various industries. From construction to automotive engineering, the unique properties of C-Glass fibers contribute significantly to enhanced performance, durability, and structural integrity.
The Foundation of Strength C-Glass Fibers
C-Glass fibers derive their name from the added component of calcium oxide (CaO) in the glass composition. This addition enhances the chemical durability and tensile strength of the fibers, making them a preferred choice for applications where resilience is paramount.
Tensile Strength
C-Glass fibers boast impressive tensile strength, making them adept at withstanding high levels of stress and strain. This characteristic is particularly crucial in industries such as construction, where materials need to endure significant loads without compromising structural integrity.
Chemical Resistance
The inclusion of calcium oxide in the glass matrix enhances the fibers’ resistance to chemical corrosion. This makes C-Glass fibers an ideal choice for applications exposed to harsh environmental conditions or corrosive substances, ensuring longevity and reliability.
Environmental Sustainability
Recyclability
C-Glass fibers exhibit recyclability, contributing to the circular economy in manufacturing. The ability to reuse these fibers in new applications reduces waste and promotes sustainable practices.
Energy-Efficient Production
The manufacturing processes involved in C-Glass fibers are designed for energy efficiency. This not only reduces the environmental footprint but also aligns with global efforts towards greener and more sustainable industrial practices.
Limitations of C-Glass Fiber
Resilient Nature of C-Glass Fiber
C-Glass fiber, known for its commendable strength and durability, has become a cornerstone in various industrial applications. From construction to automotive, its versatility is undeniable. Nevertheless, the journey is not without obstacles.
Moisture Absorption
One of the significant challenges faced by C-Glass fiber is its susceptibility to moisture absorption. This characteristic can compromise its structural integrity over time, especially in environments with high humidity levels. Engineers and manufacturers must strategize to mitigate the impact of moisture on C-Glass fiber applications.
Limited Resistance
While C-Glass fiber excels in many environments, it does face limitations when exposed to alkaline substances. This can pose a challenge in applications where resistance to alkaline corrosion is crucial. Innovations in protective coatings and chemical treatments are being explored to enhance C-Glass fiber’s compatibility in such settings.https://en.wikipedia.org/wiki/Glass_fiber
Frequently Asked Questions
Is c-glass fiber the same as regular glass fiber?
C-glass fiber is an enhanced version of traditional glass fiber. It undergoes a refining process to increase its chemical durability and mechanical strength, making it suitable for a wider range of applications.
Can c-glass fiber be recycled?
Yes, c-glass fiber is recyclable. The recycling process, however, requires specialized facilities due to its unique composition. Efforts are underway to improve and expand recycling capabilities for this versatile material.
How does c-glass fiber contribute to sustainability?
C-glass fiber’s contribution to sustainability lies in its role in lightweight construction, renewable energy, and recyclability. These aspects collectively reduce environmental impact and support sustainable practices.
Are there any limitations to the use of c-glass fiber?
While highly versatile, c-glass fiber has limitations. It may not be suitable for applications requiring extreme heat resistance, and its production process involves high energy consumption. Ongoing research aims to address these limitations.
What sets c-glass fiber apart from other reinforcing materials?
C-glass fiber stands out due to its chemical composition, offering enhanced resistance to corrosion and chemicals. This sets it apart from traditional glass fiber and other reinforcing materials, making it a preferred choice in demanding applications.
How has the demand for c-glass fiber evolved over the years?
The demand for c-glass fiber has witnessed significant growth, driven by advancements in technology and a shift towards lightweight, durable materials. Industries across the board continue to explore new applications, contributing to sustained demand.